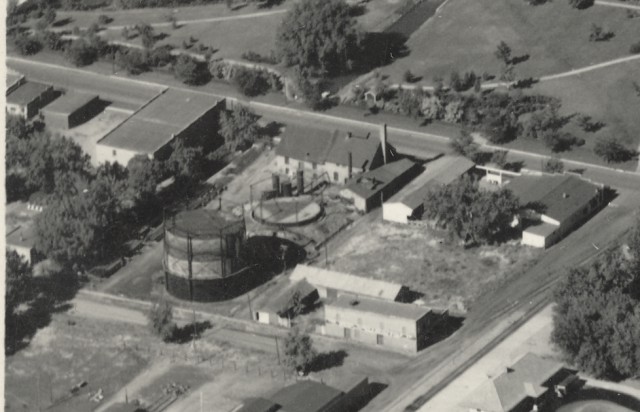
Related: Experts: Contamination from teahouse likely spread; ‘Relief holder’ may be the biggest problem of all at former town gas site; Tempest under a teacup
From the time that the first commercial gas utility was formed in London in 1812 until approximately the 1950s, there have been three primary methods for making town gas: the coal carbonization process, the oil gas process and the carburetted water gas process.
In 1902, Boulder’s 13th Street plant was built to use the coal carbonization process. In fact, the Boulder facility was extraordinary in that it was the first town-gas manufacturing facility in the world to create a successful technique for making gas from lignite, also known as soft coal. At some point in its life, probably prior to 1920, the Boulder town gas plant upgraded its equipment and began to use the carburetted water gas process to create gas with higher BTUs that was more reliable to burn.
It is important to know which processes were used at the 13th Street site because each gas-making technique creates a different fingerprint of contaminants. By knowing the process used, those evaluating and/or remediating a site can better understand what they should be looking and testing for.
According to the Heritage Research Center, other historical resources, as well as interviews with knowledgeable experts, the town gas processes used at Boulder’s 13th Street site were as follows.
The coal carbonization process used at the Boulder plant created gas by distilling the coal in heated, anaerobic vessels known as retorts. The coal was broken down into its volatile components by heating it in a nearly oxygen-free environment. As a result of this heating, some of the coal, about two-fifths, was turned into non-solids or gases. Most of the remaining coal was left as solid wastes needing disposal. The gases were then put through a device known as the hydraulic main, at which point some of the gases were converted to liquors, which consisted of contaminated water, coal tar and its associated contaminants. The remaining gas was coal gas, but at this point, it was still full of dangerous impurities.
Once out of the hydraulic main, the coal gas was put through one or more condensers and an exhauster. These cooled the gas and allowed still more coal tar and other impurities, primarily gaseous ammonia and sulfur compounds, to be removed. This process was known as washing, or purifying, the gas.
Allen Hatheway, who has examined thousands of gas works properties and who also wrote the 1,400-page book Remediation of Former Manufactured Gas Plants and Other Coal-Tar Sites, says that during the purifying process, workers would fill a purifier box or vertical “tree” purifier with lime, wood chips and/or iron oxide, then force the gas through the box or tower, allowing the materials to act as a filter. Once the materials became spent and stopped filtering out toxins, the box waste would be dumped at the plant or its nearby disposal site.
When asked how toxic the purifier wastes were, he replies, “Oh God, you wouldn’t believe it. They were the kidneys of the plant.”
Without this purifying technique, which accounts for much of the contamination left behind at town gas sites, the coal would have been less reliable to burn and also poisonous to breathe.
Once washed and cleaned, the gas was passed through the gasometer that measured it and then on to the holder (the large round tank-looking objects in photos), where it was stored until it went to the customer by way of the company’s pipelines.
The carburetted water gas process used at the Boulder plant was slightly different than coal carbonization and was considered superior because it created better burning gas. This process basically enriched coal gas by injecting oil into a vessel containing heated water, which transformed the coal gas into what was known as water gas or blue gas. Because the oil and vapor combined, the water gas had a thermal content of approximately 300 to 350 BTU per cubic foot, much superior to coal gas alone.
Carburetted water gas plants were generally made up of a brick-lined, cylindrical, steel vessel along with a generator, a carburetter and a superheater.
In this process the coal was distilled in the generator to create the original gaseous product. The gas was then drawn from the generator and pushed through a carburetor, where the oil was introduced into the vapor. This oil-gas mixture then made its way into the superheater. While in the superheater, the oil became thermally cracked and “fixed,” meaning it was completely mixed and bonded with the coal gas.
From the superheater, the water gas, as with the coal gas, was forced through sealed towers or wash boxes, where it was cooled to allow some of the coal tar wastes to settle out of the gas. The gas was then passed through one or more condensers, where impurities such as cyanide, lead, arsenic, ammonia and hydrogen sulfide were removed.
Then, the gas was passed through a scrubber, which pushed the gas through water so that still more impurities were taken out.
What this carburetted water gas process means for those now charged with cleaning up the 13th Street site is that the contaminants in play are waste products derived from both coal and petroleum. One more unfortunate thing about carburetted water gas plants is that they required a second holder known as a “relief holder.” And it is this second holder that can be the real beast when it comes to contamination onsite and in migrating groundwater (See ‘Relief holder’).
So what exactly are the contaminants of concern at the 13th Street site and other former town gas sites around the country? According to the EPA, the following are the six major classes of chemical constituents typically present at town gas sites: polynuclear aromatic hydrocarbons (PAHs); light (volatile) aromatics; phenolics; inorganic nitrogen; inorganic sulfur; and selected heavy metals.
According to the EPA, coal tars, from both the coal carbonization and the carburetted water gas processes, are complex mixtures of organic chemicals. The following are the two major classes of chemical compounds found in coal tar and are the focus of most town gas site investigations and cleanups.
The first class of contaminants is comprised of volatile organics, characterized by benzene, toluene, ethylbenzene and xylene, which are identified by their initials as the BTEX compounds.
According to the EPA and the New York State Department of Environmental Conservation, the BTEX compounds are commonly associated with gasoline, and are often encountered as contaminants surrounding leaking gasoline tanks or spills, as well as being found at former town gas sites. Together, these compounds often represent only a small percentage of the mass of town gas tar. However, of all the contaminants found in coal tar, the BTEX compounds are the most soluble and are thus the most likely to be dissolved in groundwater and migrate off site. These are also the most volatile and are thus the most likely to migrate through subsurface soils as vapors or soil gas. This soil gas tendency is important with regards to Boulder’s 13th Street site.
According to the 1994 EPA site assessment of the 13th Street plant site, virtually the entire location was covered in concrete and blacktop because it was being used as a parking lot for city employees. The EPA report notes that as long as the soil remains completely covered, any danger from soil contamination or its vapors shouldn’t be a problem. However, the report did note that any future construction that could disturb the assumed soil contamination could be a problem.
This is important on 13th Street for two reasons. First, not all of the underlying contamination is currently covered by concrete. The gardens and tree areas belonging to the teahouse and within the plaza could create direct pathways for BTEX soil gas to escape from the contaminated soil below the teahouse and plaza, into the air.
When asked about the gardens, Dushanbe Teahouse architect Vern Seieroe told BW via email, “My recollection is that the planters do not have bottoms, simply soil.”
The city has tested for benzene, and presumably the other BTEX compounds in gas form within the teahouse, and found no dangerous levels whatsoever. It is less clear if testing has been conducted in and around the planters.
The other pathway for soil contamination and its associated gases to escape from beneath the plaza and teahouse is, as noted by the EPA report, during con struction projects and remediation itself that disturb the area’s concrete cap. This occurred first when the teahouse was constructed on the site beginning in 1997. Based on photos from the time, it appears that no special health and safety precautions such as respirators or protective clothing were taken by those working in the soil at the site during construction — this despite the EPA’s 1994 report warning that the soil could be a hazard if the parking lot cap was breached.
The next potential for soil and soil gas contamination exposure came during the city’s and Xcel’s 2012 subsurface investigation activities at the site, which required sections of the parking lot to be removed, exposing the soil and former gasworks infrastructure to the air. Presumably the air was being monitored for potential contaminants during this process and was found to be safe, because photos from the 2012 excavation, as in 1997, also show workers taking no added precautions in the form of respirators or clothing.
But not all potentially hazardous contaminants were likely on the city’s and Xcel’s monitoring radar. You may recall from Part 1 of this series that Boulder Facilities and Fleet Manager Joe Castro told BW that he was unaware that heavy metals were an issue and that they had not been tested for at the site. So it is quite likely, based on the EPA’s fingerprint of contaminants at town gas sites, that cyanide, arsenic, barium, cadmium, chromium and lead are likely in the soil under the teahouse and plaza, and that they could have become airborne during excavation as well.
The second class of chemical compounds found at town gas sites, including Boulder’s 13th Street plant, are semivolatile organic compounds known as polycyclic aromatic hydrocarbons, or PAHs. PAHs are present in many forms in the environment, including asphalt and other petroleum products, such as diesel fuel. Coal tar is still commonly used today as asphalt pavement sealer. Although hundreds of PAH compounds have been identified in coal tar, the most significant of these pollutants are often referred to as the “dirty 17” by those in the business of cleaning up contamination. These 17 contaminants are recognized by the EPA as priority pollutants, and their presence is commonly used to evaluate levels of PAH contamination. The dirty 17 contaminants are acenaphthene, acenaphthylene, anthracene, benzo(a)anthracene, benzo(a)pyrene, benzo(b)fluoranthene, benzo(g,h,i)perylene, benzo(k)fluoranthene, dibenzo(a,h) anthracene., chrysene, fluoranthene, fluorine, indeno(1,2,3-cd) pyrene, 2-methylnaphthalene, naphthalene, phenanthrene and pyrene.
Each of the italicized PAHs in the above list are classified by the EPA as probable human carcinogens that are capable of causing cancer and other serious health issues in humans and animals. These carcinogens associated with town gas sites are often referred to as cPAHs.
According to the EPA and New York Department of Health and Environment, most of the PAH compounds do not readily dissolve in water, so as a rule, they are not as easily transported in groundwater as the BTEX compounds are. There is, however, one exception to this rule, naphthalene, which can move relatively quickly in groundwater. Most of the PAHs, again, unlike the BTEX compounds, do not readily volatilize in the environment, so they are not as readily transported as soil gas. However, despite low solubility and volatility, PAHs, including cPAHs, may still migrate significant distances, because mobile tars or emulsions may move through the subsurface.
All of the BTEX and PAHs contaminants listed above have been tested for at the 13th Street location where the teahouse now resides. Nearly all are present in measurable quantities, some incredibly high, as reported in the first installment in this series.
It should also be noted that the monitoring wells, which were installed to keep track of groundwater contamination associated with an earlier toxic spill at a dry cleaner some 300 feet to the southeast of the old gas site (see Part 1 of this series in Boulder Weekly, May 16, for more details on the dry cleaner site), have detected all of the BTEX compounds as well as naphthalene in the groundwater. The environmental consultant working the dry cleaner site believes that these contaminants originated from the town gas site. The city denies this offsite contamination is from the teahouse location, even though the EPA has stated that there are no other possible sources for this particular contamination footprint in the area.
As noted earlier, in addition to the BTEX and PAHs contaminants, the EPA also states that heavy metals and complex cyanides are a major contamination concern at town gas sites. These contaminants include cyanide, arsenic, barium, cadmium, chromium and lead. These pollutants do not break down and will remain in the soil until they are leached or transported offsite by groundwater. The 13th Street town gas site has not been tested for these contaminants to date, nor has the dry cleaner site been tested for these pollutants.
Such further testing could help to determine conclusively the source of various contaminants in the area — and the extent and direction to which they are migrating.
Respond: [email protected]