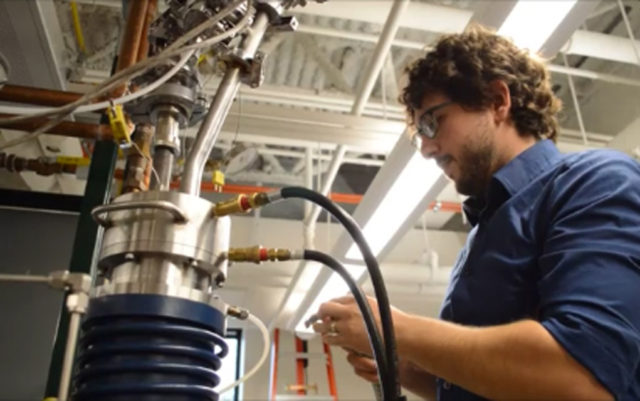
Engineers at the University of Colorado Boulder have developed a more efficient spin on an old method of processing magnesium, and it could have huge implications for the auto industry.
We usually think of a clean-running engine as the main determinant of fuel efficiency, but simply making a vehicle lighter also means it will consume less fuel. Magnesium is the perfect candidate for achieving this goal. Not only is it the lightest metal, but it is one of the top 10 most common elements found in the Earth’s crust. Yet, magnesium is usually passed over for aluminum or other metals. So why has the auto industry been ignoring it?
Magnesium, like most elements, does not exist by itself in nature. Instead, it comes in a state of raw ore, most commonly magnesia or dolomite. Processing pure magnesium out of its natural form is both energy-intensive and heavy on carbon emissions, which is where the problem lies.
Research assistant Mark Wallace explains the current processes: “You have electrolytic, which is a very clean process, but requires a bunch of energy, versus Pidgeon which is a lot easier to do but is very bad for the environment. We’re trying to find that middle ground where it’s still cost-effective and not so energy-intensive, but reducing gas emissions at the same time.”
China currently produces more than 80 percent of the world’s magnesium using the most inefficient method: the Pidgeon process. A highly energy-intensive thermal process, it yields only one ton of magnesium per 11 tons of raw material while spitting out up to 40 tons of carbon dioxide. On top of that, U.S. tariffs placed on Chinese imports bump the price of magnesium up to almost twice that of aluminum. China also uses ferrosilicon as a reduction agent to isolate magnesium, and that makes the process even more expensive.
The only magnesium production within the U.S. comes from Salt Lake City using the electrolysis process, which separates elements by running an electrical current through a salt brine of magnesium chloride. Although it is “clean” in terms of carbon emissions, it pollutes the environment with the chlorine waste left behind.
At CU’s engineering center, Dr. Aaron Palumbo has researched magnesium processing for the past three years, resulting in a potential commercial enterprise. Big Blue Technologies, named after one of the reactor furnaces, is the company growing out of Palumbo’s research with the mission to become a premier supplier of magnesium in the United States.
During World War II, the U.S. produced magnesium out of necessity to supply weapons and artillery manufactories, but profitability soon declined after the war and production was halted. However, the process used during this time provided the backbone for CU’s research team to develop a new and vastly improved version of the production method. Their study describes it as carbothermal reduction, which uses carbon as the reacting agent instead of ferrosilicon.
The Big Blue Technologies method promises to use less than half the energy (30 megawatt hours) of the dominant Pidgeon process (60-90 Mwh) and to emit about 50 percent less carbon dioxide.
According to Palumbo, using carbon in the process will also make magnesium available at a much cheaper price, which is where the auto industry comes into play.
“Is there a current demand for it? No. But it has a lot of potentials,” says Dr. Fadi Abufarha, associate professor at Clemson University’s International Center for Automotive Research. “If this process is really developed and it can produce magnesium at a lower cost, then there would be significant demand for magnesium.”
The material is already alloyed with aluminum and used in structural components of cars, but the more magnesium used, the lighter the car will be. According to Abufarha, every 10 percent of mass reduced saves 6 percent of fuel consumption.
Wallace hopes that auto manufacturers would switch over to magnesium if they had a steady supply, reducing energy use and emissions all around.
“Our process, if we can get a continued process working, beats everything currently available on the market on both energy and emissions,” he says.
As it grows, Big Blue Technologies hopes to remain based in Colorado and is embarking on the challenge of scaling the prototype up to industrial size. The company has reached out to Nevada Clean Magnesium, Inc. as a potential provider for dolomite, magnesium’s natural form.
For now, Big Blue Technologies and its processing method remains in the lab, but Palumbo, Wallace and other researchers continue to work to get their idea off the ground.